Composite piping has become an increasingly popular alternative to traditional steel piping in various industries, including oil and gas, chemical processing, and water treatment. This shift is driven by numerous advantages that composite materials offer over steel. These advantages span areas such as corrosion resistance, weight reduction, ease of installation, durability, cost-effectiveness, and environmental impact. This article delves into these benefits, highlighting why composite piping is emerging as the preferred choice for many applications.
Corrosion Resistance
One of the most significant advantages of composite piping over steel is its exceptional resistance to corrosion. Steel pipes, especially when exposed to harsh environments or aggressive chemicals, are prone to rust and corrosion. This degradation can compromise the structural integrity of the piping system, leading to leaks, failures, and costly repairs.
In contrast, composite pipes are made from materials like fiberglass, carbon fiber, or a combination of resins and reinforcing fibers that are inherently resistant to corrosion. These materials do not react with most chemicals and can withstand exposure to a wide range of corrosive substances, including acids, bases, and salts. This makes composite piping particularly suitable for applications in chemical processing plants, offshore oil and gas operations, and wastewater treatment facilities, where exposure to corrosive agents is common.
Weight Reduction
Composite pipes are significantly lighter than steel pipes. This weight reduction offers several advantages, including easier handling, reduced transportation costs, and simpler installation procedures. For instance, in large-scale construction projects or offshore installations, the lightweight nature of composite piping can lead to substantial savings in labor and equipment costs. Moreover, the reduced weight minimizes the structural load on supporting infrastructure, which can be particularly beneficial in applications such as shipbuilding and aerospace.
Ease of Installation
The lighter weight and flexibility of composite piping translate to easier and faster installation compared to steel piping. Composite pipes can be manufactured in longer lengths, reducing the number of joints and connections needed. This not only speeds up the installation process but also reduces the potential for leaks at connection points.
Furthermore, composite pipes can be easily cut, shaped, and joined using simple tools, without the need for specialized welding equipment required for steel pipes. This ease of installation can be especially advantageous in remote or hard-to-reach locations where access to heavy machinery and skilled labor is limited.
Durability and Longevity
Composite pipes offer superior durability and a longer lifespan compared to steel pipes. They are resistant to a wide range of environmental factors, including ultraviolet (UV) radiation, temperature fluctuations, and mechanical stress. Unlike steel pipes, which can become brittle or weaken over time due to corrosion and wear, composite pipes maintain their structural integrity and performance over extended periods.
The high strength-to-weight ratio of composite materials also means that composite pipes can withstand high pressures and mechanical loads without deforming or breaking. This makes them suitable for demanding applications such as high-pressure gas transmission, deep-sea oil exploration, and high-rise building plumbing systems.
Cost-Effectiveness
While the initial cost of composite piping can be higher than that of steel pipes, the overall lifecycle cost is often lower. The reduced need for maintenance, repairs, and replacements due to the corrosion resistance and durability of composite pipes can lead to significant cost savings over time. Additionally, the ease of installation and reduced labor costs further contribute to the cost-effectiveness of composite piping systems.
In many cases, the longer lifespan and lower maintenance requirements of composite piping can offset the higher upfront investment, making it a more economical choice in the long run.
Thermal and Electrical Insulation
Composite materials have inherent thermal and electrical insulating properties, which can be advantageous in certain applications. Steel, being a good conductor of heat and electricity, can pose challenges in situations where insulation is required to prevent heat loss, condensation, or electrical hazards.
Composite pipes, on the other hand, provide effective thermal insulation, helping to maintain the temperature of the transported fluids and reducing energy losses. This is particularly important in applications such as district heating systems, hot water distribution, and chilled water lines.
The electrical insulating properties of composite materials also make composite pipes suitable for use in environments where electrical conductivity needs to be minimized, such as in proximity to high-voltage electrical equipment or in corrosive environments where stray currents can accelerate corrosion in metal pipes.
Environmental Impact
Composite piping systems offer several environmental benefits over steel pipes. The production of composite materials typically generates lower carbon emissions compared to steel manufacturing, which involves energy-intensive processes and significant greenhouse gas emissions. Additionally, the longer lifespan and reduced maintenance requirements of composite pipes result in less frequent replacements and lower resource consumption over time.
Furthermore, many composite materials can be recycled or repurposed at the end of their service life, reducing the environmental impact associated with disposal. Advances in composite manufacturing techniques are also leading to the development of more sustainable materials and processes, further enhancing the environmental credentials of composite piping systems.
Versatility and Customization
Composite pipes can be engineered to meet specific performance requirements by varying the types and proportions of resins and reinforcing fibers used. This versatility allows manufacturers to tailor composite piping systems to suit a wide range of applications and operating conditions.
For example, composite pipes can be designed to offer enhanced resistance to specific chemicals, increased strength for high-pressure applications, or improved flexibility for easy installation in complex layouts. This level of customization is difficult to achieve with steel pipes, which have more limited material properties and design options.
Noise and Vibration Damping
Composite materials have excellent damping properties, which help to reduce noise and vibrations in piping systems. Steel pipes, being rigid and heavy, can transmit vibrations and noise generated by fluid flow, pumps, or other mechanical equipment. This can lead to operational issues, noise pollution, and discomfort in residential or commercial buildings.
Composite pipes, due to their flexible and non-metallic nature, can absorb and dampen these vibrations, resulting in quieter and smoother operation. This is particularly beneficial in applications such as HVAC systems, plumbing in residential buildings, and industrial piping systems where noise reduction is a priority.
Improved Safety
The combination of corrosion resistance, durability, and electrical insulation properties of composite pipes contributes to improved safety in various applications. For instance, in chemical processing plants, the use of composite piping reduces the risk of leaks and spills caused by corrosion, enhancing the overall safety of the facility.
In environments where electrical hazards are a concern, the non-conductive nature of composite materials helps to mitigate the risk of electrical shocks and short circuits. Additionally, the lighter weight of composite pipes reduces the risk of injury during handling and installation, contributing to a safer working environment for construction and maintenance personnel.
Conclusion
Composite piping offers a multitude of advantages over traditional steel piping, making it an increasingly popular choice across various industries. The superior corrosion resistance, reduced weight, ease of installation, durability, cost-effectiveness, and environmental benefits of composite materials position them as a viable and often preferable alternative to steel. As technology advances and the demand for high-performance, sustainable piping solutions grows, the adoption of composite piping systems is expected to continue to rise, driving innovation and improving infrastructure resilience and efficiency.
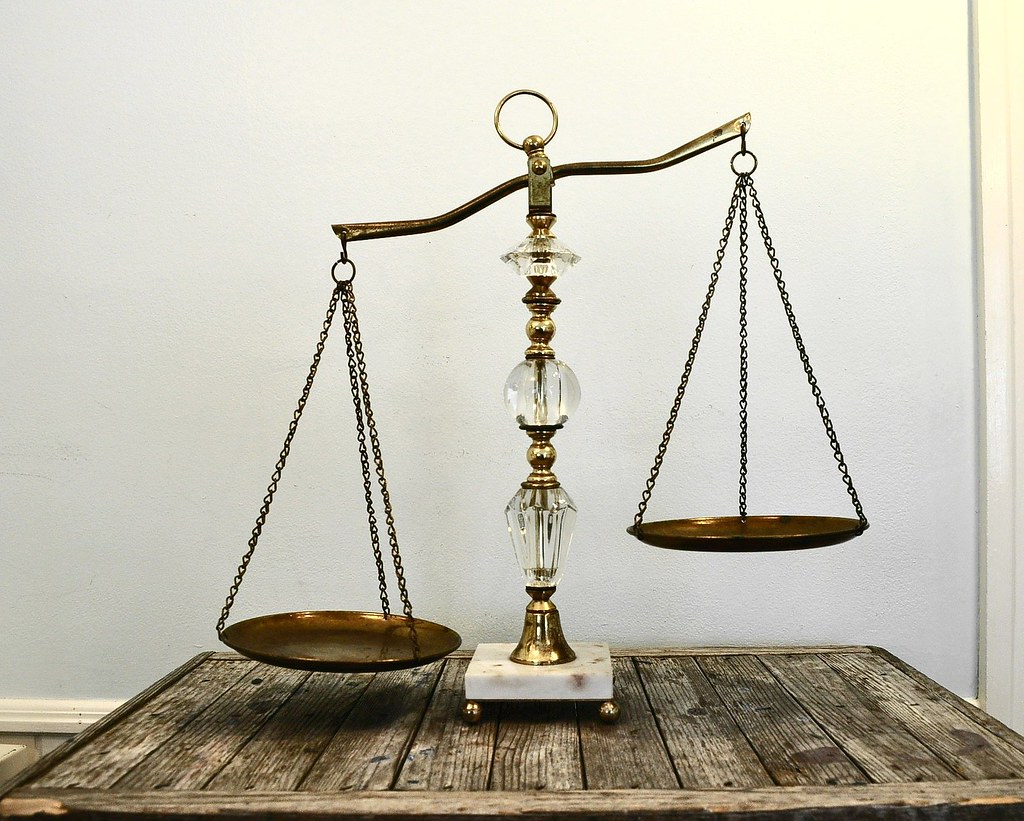